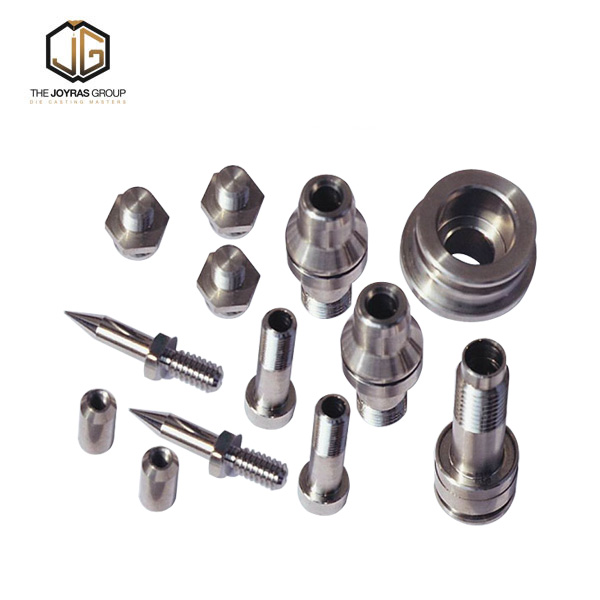
What are the skills required for machining jobs?
Machining is a technical field that requires specific skills and knowledge. Some of the critical skills required for machining jobs include:- Proficiency with machine tools: A machinist should have a good understanding of different machines such as lathes, mills, and grinders, and how to operate them. They should also have knowledge of cutting tools, feeds, and speeds to achieve the required precision.
- Knowledge of materials: A machinist should have in-depth knowledge of various materials, including metals, plastics, and composites, on how to machine them effectively.
- Read blueprints: A machinist should be able to understand and interpret engineering blueprints and drawings to produce the required dimensions and tolerances.
- Math skills: Precision machining requires strong math skills, including algebra, geometry, and trigonometry. Machinists must be able to perform complex calculations, including dimensional measurements and tolerances.
- Attention to detail: Machining requires a high level of precision. The machinist should pay attention to every detail to ensure that the final product meets the necessary specifications.
What is the significance of the machining process?
Machining is significant in the manufacturing industry as it allows the creation of complex parts with high precision and accuracy. The process has several advantages, including:- Production of high-quality and precise parts.
- The ability to manufacture complex parts that cannot be produced using other manufacturing processes such as casting and forging.
- Cost-effectiveness: Machining allows for the production of parts in large volume, reducing the per-unit production cost.
What are the types of machining processes?
Some of the common machining processes include:- Turning: This is a process that involves the rotation of the workpiece while a cutting tool moves in a linear motion to remove materials from the workpiece.
- Milling: This is a process that involves rotating the cutter along multiple axes to remove materials from the workpiece.
- Drilling: This is the process of creating holes in the workpiece using a rotating tool.
- Grinding: This is a process that involves the use of an abrasive material to remove small amounts of materials from the workpiece.
In conclusion, machinists play a crucial role in the manufacturing industry. They are responsible for creating complex parts with high precision and accuracy. It requires specific skills and knowledge to become a machinist, including proficiency with machine tools, knowledge of materials, and good math skills. Machining has several advantages, including the production of high-quality parts and cost-effectiveness.
Joyras Group Co., Ltd. is a leading manufacturer of CNC machines for different industries. Our machines are designed to deliver high precision and accuracy, and we have an excellent team of experienced machinists who can handle any project. Visit our website https://www.joyras.com for more information on our products and services. For inquiries, contact us via email at sales@joyras.com.
Scientific Papers
1. Colby, T., 2013. "Recent Advances in Machining Processes," International Journal of Machine Tools and Manufacture, vol. 53, no. 1, pp. 39-55.
2. Wu, Y., et al., 2016. "A Study on Machining Parameters Optimization in Milling Processes," Journal of Manufacturing Science and Engineering, vol. 138, no. 6, pp. 554-562.
3. Davis, M., et al., 2018. "Effects of Cutting Parameters on Surface Integrity in Turning Processes," Journal of Materials Processing Technology, vol. 256, pp. 49-57.
4. Chen, H., et al., 2015. "Tool Wear and Tool Life Analysis in Drilling Processes," Wear, vol. 322-323, pp. 154-163.
5. Jung, J. H., et al., 2017. "Investigation of Surface Roughness in Grinding Processes," Journal of Mechanical Science and Technology, vol. 31, no. 2, pp. 947-956.
6. Xu, J., et al., 2014. "A Study on the Micro-Milling of Hardened Steel," International Journal of Advanced Manufacturing Technology, vol. 73, no. 1, pp. 265-273.
7. Wang, H., et al., 2019. "Effects of Cutting Parameters on the Chip Formation and Surface Quality in Milling Processes," Mechanism and Machine Theory, vol. 132, pp. 296-305.
8. Liao, Y., et al., 2015. "A Comprehensive Study of Tool Wear in Turning Processes," Wear, vol. 324-325, pp. 112-123.
9. Lee, J., et al., 2016. "A Study on the Optimal Machining Conditions in Drilling Processes," Journal of Mechanical Science and Technology, vol. 30, no. 9, pp. 4015-4022.
10. Zhang, J., et al., 2014. "Surface Roughness Improvement in Grinding Processes Using Ultrasonic Assisted Grinding," International Journal of Advanced Manufacturing Technology, vol. 75, no. 9-12, pp. 1811-1822.