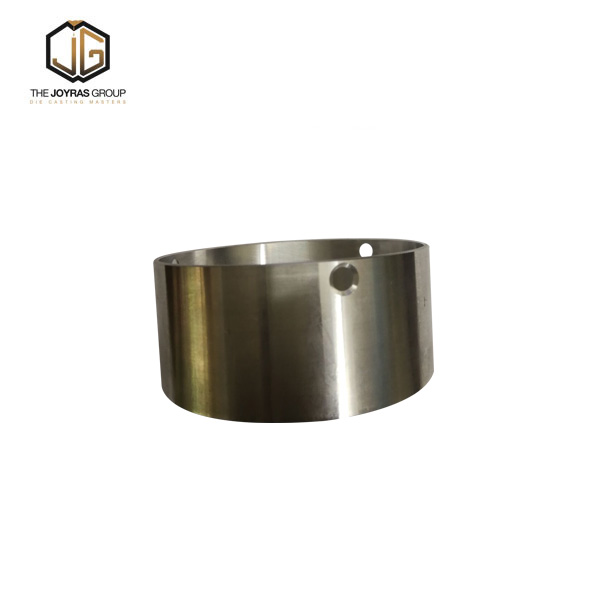
What materials are commonly used to manufacture Extrusion Parts?
Extrusion Parts can be made from a range of materials, including aluminum, titanium, stainless steel, and plastic. The choice of material depends on the application and the environment in which the component will be used. For example, aluminum is lightweight and has good thermal conductivity, making it ideal for use in applications where heat dissipation is important.How is the quality of Extrusion Parts ensured?
Manufacturers of Extrusion Parts use various quality control measures to ensure that the components meet the required specifications. These measures include visual inspections, dimensional checks, and testing for strength and durability. In addition, manufacturers may use computer simulations to predict the behavior of Extrusion Parts under different conditions.What are some common applications of Extrusion Parts?
Extrusion Parts are used in various applications, such as in the construction of buildings, bridges, and other structures. They are also used in the automotive industry for the production of parts such as engine blocks, wheels, and suspension components. In addition, Extrusion Parts are used in the production of aerospace components such as aircraft frames and wings.In conclusion, Extrusion Parts are a critical component in many industries due to their strength, durability, and resistance to harsh environments. Manufacturers use various quality control measures to ensure that these components meet the required specifications. With the increasing demand for Extrusion Parts in various industries, it is important for manufacturers to continue to innovate and improve their processes to produce cost-effective and reliable components.
Joyras Group Co., Ltd. is a leading manufacturer of Extrusion Parts. With years of experience and a commitment to quality, we are dedicated to providing our clients with cost-effective and reliable components. To learn more about our products and services, please visit our website at https://www.joyras.com. For inquiries, please contact us at sales@joyras.com.
Papers on Extrusion Parts:
1. D. Liu, Y. Zhang, and H. He, (2016). “Process parameter optimization on metal extrusion forming,” Journal of Materials Processing Technology, vol. 238, pp. 410-416.
2. S. Lee, D. Kim, and J. Kim, (2018). “Design and analysis of aluminum extrusion for electric vehicle body,” Applied Science, vol. 8, no. 9, pp. 1739.
3. R. Kumar, S. Kumar, and B. Sharma, (2015). “Effect of extrusion speed on aluminum alloy AA6082,” Journal of Materials Engineering and Performance, vol. 24, no. 12, pp. 4705-4711.
4. P. Singh, (2017). “Influence of die angle on extrusion load and surface roughness,” International Journal of Engineering and Technology, vol. 9, no. 1, pp. 1739-1743.
5. R. Singh, S. Sharma, and R. Chauhan, (2019). “Finite element analysis of multi-hole extrusion for composite materials,” Materials Science and Engineering, vol. 668, pp. 012083.
6. A. Perez-Bergquist and J. Bayless, (2018). “Aluminum extrusion design for energy absorption,” SAE Technical Paper, no. 2018-01-0116.
7. V. K. Sharma and A. Kumar, (2016). “Investigation of material flow during hot extrusion of magnesium alloy,” International Journal of Advanced Manufacturing Technology, vol. 86, pp. 1579-1596.
8. T. K. Gupta, (2016). “Finite element simulation of aluminum tube extrusion,” Proceedings of the Institution of Mechanical Engineers, Part B: Journal of Engineering Manufacture, vol. 230, pp. 1204-1212.
9. J. Zhao, J. Yang, and L. Zhang, (2015). “Simulation and experiment on the extrusion forming of aluminum profile,” Procedia Engineering, vol. 81, pp. 726-731.
10. M. Singh and K. Singh, (2017). “Influence of die design on surface roughness in aluminum alloy extrusion,” International Journal of Engineering and Technology, vol. 9, no. 6, pp. 4543-4546.